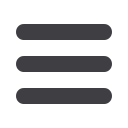
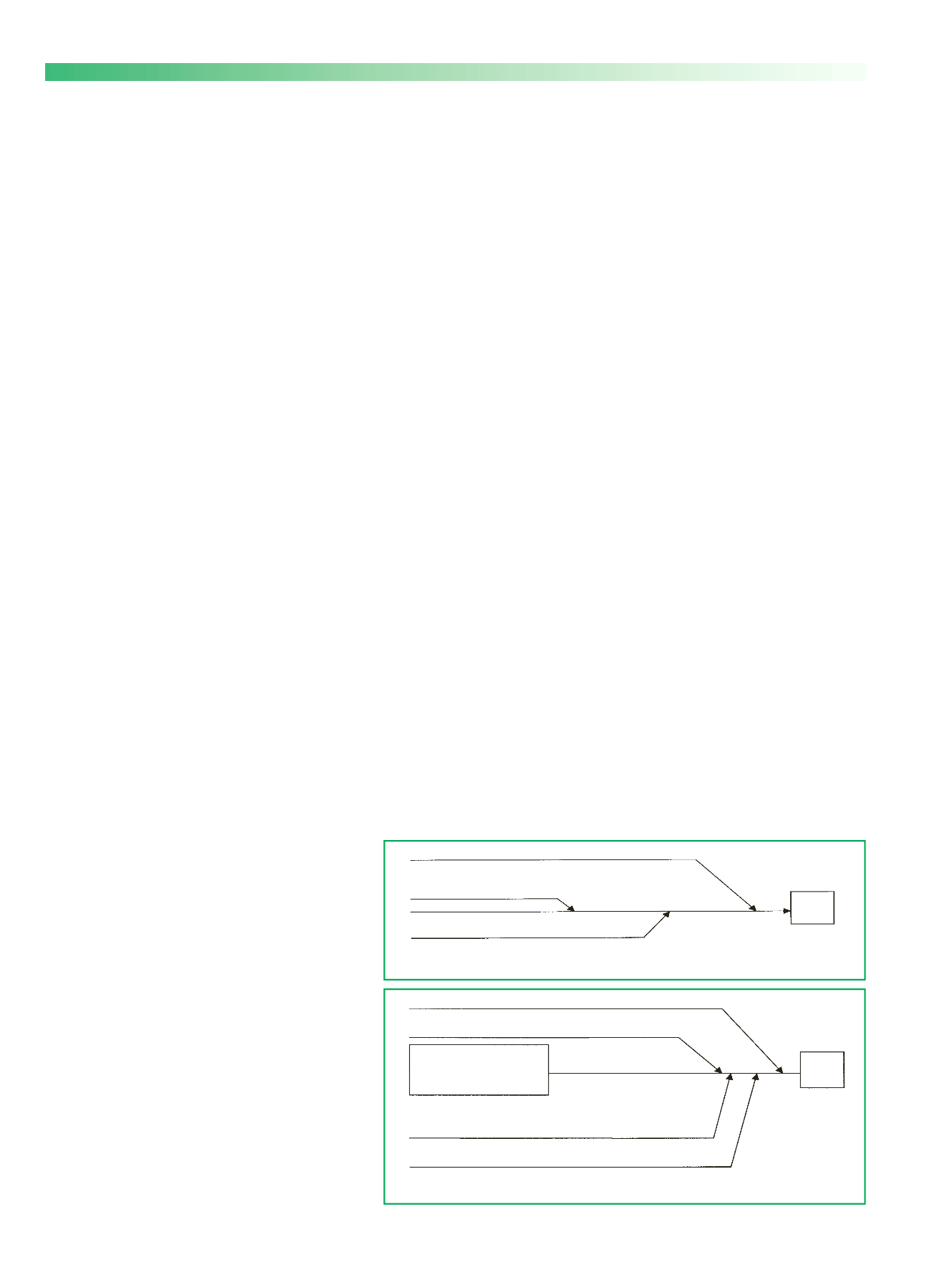
20
ЭКОНОМИКА И УПРАВЛЕНИЕ
ПИЩЕВАЯ ПРОМЫШЛЕННОСТЬ
4/2006
Качество продукции формируется на
стадиях ее жизненного цикла в соот+
ветствии с требованиями системы ме+
неджмента качества (СМК). На каждой
стадии жизненного цикла продукции
предусмотрен контроль качества, и в
том числе работы по анализу рисков.
Анализ риска – процесс сбора и оцен+
ки информации для выявления потен+
циально опасных факторов и условий,
приводящих к их возникновению [1].
Технологическая подготовка производ+
ства, уровень ресурсного обеспечения,
уровень технологии и организации,
уровень исполнителей должны обеспе+
чить нормируемое качество продук+
ции, которое впоследствии будет оце+
нено потребителями [2].
Управлять качеством – значит уметь
решать проблемы системно, анализи+
руя исходную информацию о продук+
ции и производстве [3, 4].
Основные причины снижения каче+
ства работы:
1.
Технологические
:
ошибки в заданиях (заказ+нарядах,
заявках);
выпуск негодной продукции и затра+
ты на доводку качества (акции по ис+
правлению заводских дефектов).
2.
Экономические
:
недостаток запаса запчастей, рас+
ходных материалов и комплектующих,
приводящие к простоям производства;
высокий процент просроченных пла+
тежей;
ошибки в отчетности, в платежных
документах.
3.
Информационные
:
ошибки в отчетах, программах, тех+
нологических картах;
исправления в текстах некоторых до+
кументов (например, технологических
инструкциях);
неполный объем и неточность ин+
формации;
языковой барьер при работе с тех+
нической и другой документацией;
длительное время получения инфор+
мации.
4.
Маркетинговые
:
низкая точность прогнозных допуще+
ний;
неправильное составление заказов,
ошибки в контрактах;
большой очереди на обслуживание
или отсутствие клиентов и др.
После определения основных при+
чин снижения качества необходимо
перейти к постановке следующей зада+
Влияние производственных
проблем на качество продукции
чи в процессе непрерывного совер+
шенствования и развития предприятия.
Эта задача – выявление и устранение
первопричин. Результативными могут
быть только те меры, которые воздей+
ствуют именно на первопричины оши+
бок, а значит, направлены на устране+
ние возможности повтора ошибок. В
современной практике управления к
числу проблем качества относят не
только случаи брака, дефектности, но
и невостребованность товара; потери
из+за простоев, превышение норм рас+
хода ресурсов, содержание излишних
страховых запасов и другие ошибоч+
ные результаты.
Согласно принципу Парето, среди
множества потенциальных причин, по+
рождающих следствие, лишь одна–две
являются существенными. Необходимо
организовать поиск именно этих при+
чин. Другими словами, первопричиной
следует считать ту, устранение которой
обеспечивает коренное исправление
нежелательной ситуации. Поэтому для
обеспечения непрерывного и успешно+
го развития любой деятельности необ+
ходимо отработать технологию поиска
первопричин, превратить ее в систему
и возвести в один из основополагаю+
щих принципов управления.
Для поиска первопричин можно ис+
пользовать причинно+следственную
диаграмму Исикавы [5]. Она позволя+
ет систематизировать все потенциаль+
ные причины, выделить из них суще+
ственные и провести поуровневый по+
иск первопричин. Рассмотрим это на
примере производственной деятель+
ности какого+либо перерабатывающе+
го предприятия. На данном предприя+
тии бракуется конечная продукция из+
за несоответствия ее требованиям
нормативных документов. Проведем
анализ этого вида дефекта (Д). На
первом этапе надо установить наибо+
лее вероятную зону причин дефектно+
сти (рис. 1).
Предположим, статистические дан+
ные или экспертные оценки подтвер+
дили, что наиболее вероятная зона
(80 %) исследуемого вида дефекта –
некачественное производство работ.
Однако на этом этапе анализ не может
быть завершен, так как еще нет воз+
можности принять конкретные конст+
руктивные меры по устранению де+
фектности. Продолжим поиск причин
дефектов в выявленной зоне на пер+
вом уровне (рис. 2).
Из рис. 2 видно, что основная причи+
на первого уровня – физически и мо+
рально изношенное оборудование,
хотя дополнительно обращает на себя
внимание и нарушение технологии ра+
ботниками (20 %). Продолжение по+
уровневого поиска первопричин де+
фектов показано на рис. 3, 4.
Из рис. 3 видно, что преобладают
причины, связанные с отказами обору+
дования (78 %). Однако и нарушения
технологической дисциплины (20 %)
также оказывают влияние на выпуск
бракованной продукции на предприя+
тии (на рис. 2 эта причина также была
отмечена).
Из рис. 4 видно, что низкая рента+
бельность производства, высокая теку+
честь кадров и неудовлетворительные
условия труда провоцируют причины
третьего и второго уровней, а это в ко+
О.Л. Сороко
Белорусский государственный аграрный технический университет, г. Минск
Рис. 1. Зона причин дефектов
Некачественная исходная информация (13 %)
Некачественные исходные материалы (7 %)
Некачественное производство работ (80 %)
Д
Низкая организация работ (20 %)
Рис. 2. Поиск причин первого уровня
Некачественная исходная информация (6 %)
Нарушения технологии работниками (20 %)
Некачественное
производство
работ
Несовершенное (физически и морально изношенное)
оборудование (54 %)
Д
Электронная Научная СельскоХозяйственная Библиотека