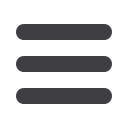
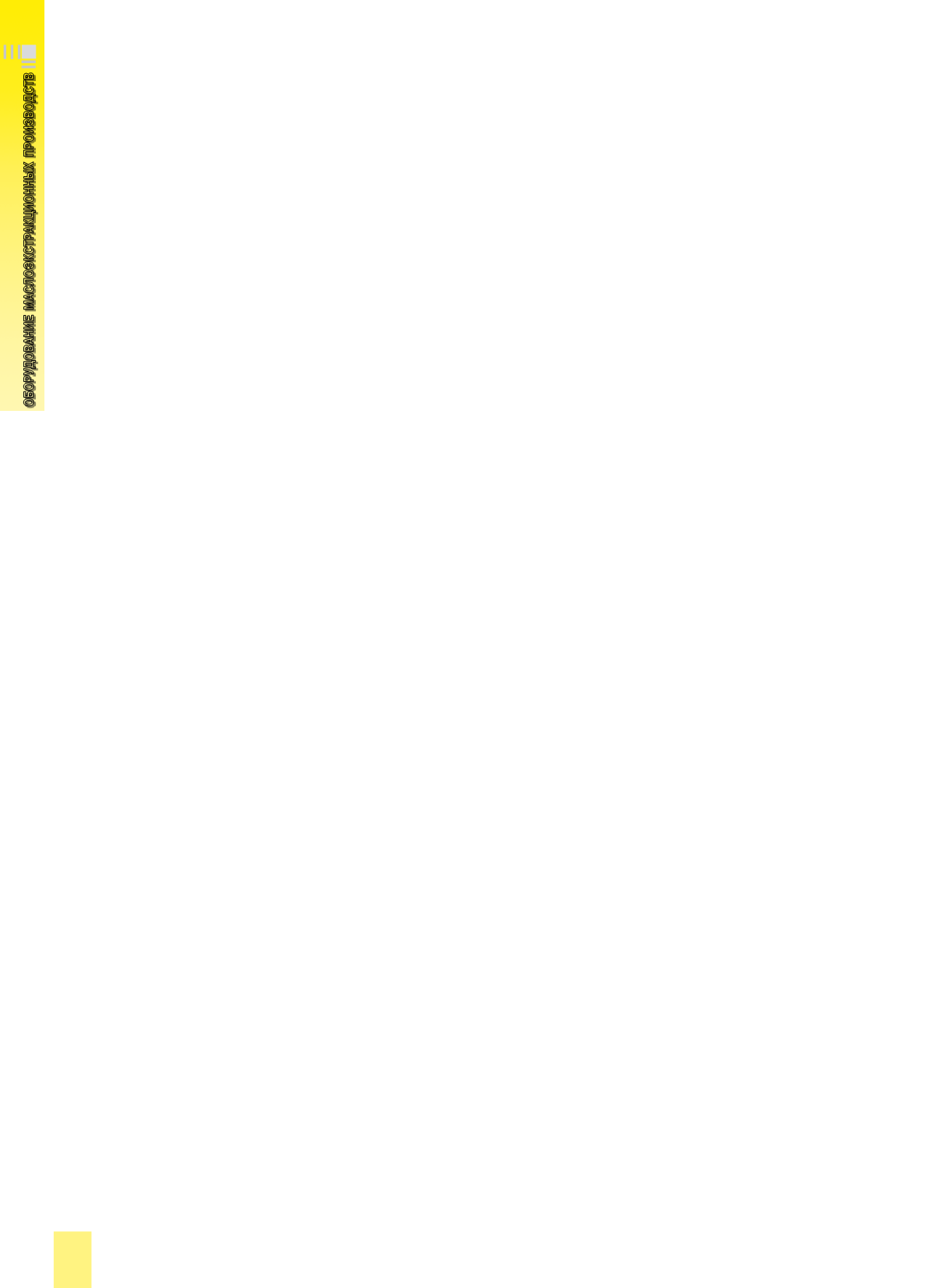
14
МасложироваЯ промышленность
№ 6-2013
оборудование маслоэкстракционных производств
дистиллятора. В качестве теплоноси-
теля используется как свежий насы-
щенный водяной пар, так и вторичные
отходящие пары от других стадий
производства. Как правило, на пер-
вой ступени дистилляции применя-
ется смесь паров растворителя и во-
дяного пара, выходящая из аппарата
для отгонки растворителя из проэк-
страгированного материала – шрота.
Для чистого водяного пара в литера-
турных источниках приведены мето-
дики расчета и значения коэффици-
ента теплоотдачи при конденсации
для наших давлений и температур
около 10000 Вт
⋅
м
–2
.
К
–1
. Что же каса-
ется конденсации смеси паров ве-
ществ, применяемых в маслоэкстрак-
ционном производстве, то данных по
этому вопросу крайне мало и одно-
значного ответа о величине коэффи-
циента теплоотдачи обнаружить не
удалось. Это обусловлено, в первую
очередь, сложностью решения такой
задачи, особенно это касается наше-
го случая, когда компоненты смеси –
водяной пар и пары растворителя не
являются взаимно растворимыми.
Но все же, исходя из общей теории
конденсации, величина коэффициен-
та теплоотдачи может быть прибли-
женно вычислена, и она очень высока
по сравнению с другими составляю-
щими уравнения (1).
Интенсификация теплообмена со
стороны греющего теплоносителя
возможна в основном за счет разру-
шения или срыва пленки конденсата
с наружной поверхности трубок для
более активного вовлечения в про-
цесс новых порций пара. Важно так-
же как можно быстрее отводить кон-
денсат из полости аппарата через
конденсатоотводчики.
Вторая составляющая уравнения (1)
характеризует передачу тепла через
стенку трубки. Здесь все определяется
теплопроводностью материала трубки,
ее толщиной, загрязнениями, иными
словами – конструкционными свойства-
ми аппарата и применяемыми техноло-
гическими режимами.
Здесь есть резервы повышения эф-
фективности за счет возможности при-
менения тонкостенных трубок из ма-
териалов, обеспечивающих конструк-
ционную прочность аппаратов. Также
в перспективе возможно применение
принципиально новых материалов с
заданными высокими анизотропными
тепловыми свойствами.
Значимым препятствием для
теплопередачи могут быть и от-
ложения, образовывающиеся на
внутренней стенке трубы. Их не-
обходимо регулярно удалять при
планово-предупредительных ремон-
тах, а лучше не допускать их большо-
го образования за счет организации
тщательной фильтрации мисцеллы,
увеличения скорости движения мис-
целлы по трубкам.
Третья величина коэффициента те-
плоотдачи со стороны мисцеллы вну-
три трубки, по нашим данным, может
изменяться в очень широком диапа-
зоне от 50 до 3000 Вт
⋅
м
–2
.
К
–1
. Эта ве-
личина существенно зависит от кон-
центрации мисцеллы, температуры,
паросодержания двухфазного потока,
скорости движения фаз, геометрии ка-
нала и его ориентации в пространстве,
а для вертикальных труб – направления
движения мисцеллы.
В любом случае величина коэф-
фициента теплопередачи определя-
ется, в основном, коэффициентом
теплоотдачи со стороны обрабаты-
ваемой жидкости – мисцеллы. Поэ-
тому наибольший эффект с позиции
энергосбережения может дать ин-
тенсификация тепло- и массообмена
именно здесь.
Интенсификация теплообмена при
кипении жидкостей обеспечивает не
только рост теплоотдачи и увеличе-
ние максимального теплового потока,
а также соответствующих критических
температурных напоров и смещение
кипения в область более высоких тем-
пературных напоров и тепловых пото-
ков. Отметим, что возможности интен-
сификации теплообмена при кипении
намного больше, чем в однофазных
потоках. Так, коэффициент теплооб-
мена кипящих движущихся сред уда-
ется увеличить до десяти раз. Наряду
с турбулизаторами, закручивающими
устройствами, оребрением для интен-
сификации теплообмена при кипении
используют нанесение на поверхность
тонких покрытий из материала с низ-
кой теплопроводностью или пористого
материала, устанавливают неизотер-
мические ребра, используют шерохо-
ватые поверхности.
Способов интенсификации тепло-
обмена разработано и применяется
достаточно много. Их можно разде-
лить на конструкционные и режим-
ные. У каждой группы есть свои до-
стоинства и недостатки.
Из конструкционных способов ин-
тенсификации самым очевидным явля-
ется изменение структуры поверхности
теплообмена. Наличие на поверхности
волн, ребер, лунок и т.п. существенно
влияет на интенсивность теплоотдачи.
Но это, как правило, значительно удо-
рожает стоимость изготовления множе-
ства трубок, а значит, и аппарата в це-
лом. Так как мы имеем дело с кипящей
жидкостью, то привлекательным может
показаться метод применения поверх-
ностей с микронеровностями для до-
полнительного стимулирования цен-
тров парообразования, это применимо
в основном для чистых жидкостей.
Очень перспективным может быть
применение интенсификаторов в
виде регулярных или нерегулярных
пространственных конструкций, вво-
димых вовнутрь трубок. Остается
открытым вопрос об увеличении ги-
дравлического сопротивления ка-
нала, а значит, и о дополнительных
энергозатратах на перемещение
жидкости.
С помощью этих способов удается
увеличить теплопередачу в 2–3 раза,
но расчет эффективности должен
учитывать стоимость самих конструк-
ций и применяемых материалов, до-
полнительные затраты на перекачку
мисцеллы, а также расходы на более
квалифицированное обслуживание
К режимным методам интенси-
фикации относятся такие, которые
позволяют, не прибегая к конструк-
ционным модификациям аппаратов,
добиться улучшения теплогидроди-
намической обстановки. Например,
возможен дополнительный вдув газа
на входе в канал.
Как показывает накопленный опыт,
хорошим техническим приемом явля-
ется рециркуляция, т. е. многократное
полное или частичное возвращение
потока обрабатываемой мисцеллы в
технологический процесс с целью ре-
гулирования температуры, концентра-
ции масла, увеличения выхода готово-
го продукта.
Для организации рециркуляции
требуется дополнительная переоб-
вязка дистиллятора и установка насо-
са. Для правильного решения инже-
Электронная Научная СельскоХозяйственная Библиотека