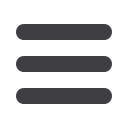

12
МасложироваЯ промышленность
№ 6-2013
оборудование маслоэкстракционных производств
Энергосбережение требует все
более и более тщательного поиска
резервов экономии ресурсов на всех
стадиях производства растительного
масла. Причем, как правило, при сни-
жении энергопотребления выявляют-
ся возможности повышения произво-
дительности оборудования и улучше-
ния качества выпускаемой продукции.
В этом смысле одной из самых пер-
спективных стадий маслодобывания
является дистилляция мисцеллы.
Удельные энергозатраты здесь внуши-
тельные. Нагреваются и переводятся
в газообразное состояние и затем
конденсируются большие массы жид-
кости. При этом нагрев нужно вести
с осторожностью, избегая локальных
и даже кратковременных перегревов
масла в мисцелле из-за высокой тер-
молабильности, как самого масла, так
и содержащихся в нем сопутствующих
веществ. От режимов применяемых
тепло- и массообменных процессов
на стадии маслодобывания во многом
зависит последующий процесс ра-
финации и выход рафинированного
масла, а также его качество. Как итог
– обоснование, проверку и выбор ме-
тодов интенсификации тепло- и мас-
сообмена и, соответственно, требуе-
мые технологические параметры про-
цессов следует увязывать не только с
физико-химическими свойствами уча-
ствующих в процессах веществ, но и
с качественными показателями полу-
чаемых масел. Без сомнения важней-
шими остаются вопросы взрыво- и по-
жаробезопасности при эксплуатации
оборудования.
Дистилляционное оборудование
относится к категории теплообмен-
ного оборудования. Для глубокого
понимания процессов, происходя-
щих внутри аппаратов, необходимы
теоретические и эксперименталь-
ные исследования свойств веществ
в жидком и газообразном состоя-
нии. Наличие всех видов тепло- и
массообмена в заданном техноло-
гическими параметрами диапазоне
температур и давлении, включая об-
ласти фазовых переходов, услож-
няет задачу. Численное и натурное
моделирование теплофизических
процессов позволяет произвести
расчет и проектирование нового
теплотехнического оборудования
или открыть новые возможности уже
эксплуатируемого.
Экспериментальные и теорети-
ческие исследования необходимы
для обоснования методов расчета
термодинамических и переносных
свойств в различном агрегатном со-
стоянии, выявления механизмов пе-
реноса массы, импульса и энергии
при конвекции, физико-химических
превращениях.
На первых ступенях дистилляции
при обработке мисцеллы в трубах
дистилляторов должен быть органи-
зован устойчивый режим, при кото-
ром достигается максимальная эф-
фективность процесса. Надежным
и проверенным способом остается
рециркуляция. На наш взгляд этому
техническому приему уделяется не-
достаточно внимания как со стороны
исследователей, так и со стороны
производственных специалистов.
По классическому определению
рециркуляция – многократное пол-
ное или частичное возвращение по-
тока веществ в технологический про-
цесс с целью регулирования темпе-
ратуры, концентрации компонентов в
смесях, увеличения выхода целевого
вещества, в нашем случае концен-
трированной мисцеллы.
Чем же все-таки привлекательна ор-
ганизация рециркуляции? Во-первых,
без изменения конструкции аппарата
с минимальными затратами можно вы-
бирать наиболее эффективный режим
движения газо-жидкостного потока,
при котором достигается максималь-
ная теплопередача. Во-вторых, суще-
ственно облегчается управление тех-
нологическим процессом за счет со-
кращения определяющих параметров.
В-третьих, как следствие, открываются
широкие возможности для простой ав-
томатизации процесса. В-четвёртых,
практически исключается возможность
образования зон локального перегрева
обрабатываемой мисцеллы, что, несо-
мненно, отражается на качестве полу-
чаемых масел.
В каждой трубе дистиллятора ин-
тенсивность теплообмена определя-
ется коэффициентом теплопередачи
от греющего пара через стенку тру-
бы к мисцелле:
,
(1)
где
α
1
и
α
2
– коэффициенты теплоот-
дачи снаружи и внутри трубы соот-
ветственно, Вт
⋅
м
–2
.
К
–1
;
δ
ст
– толщина
стенки трубы, м;
λ
ст
– коэффициент
теплопроводности материала труб-
ки, Вт
⋅
м
–1
.
К
–1
;
δ
отл
– толщина отло-
жений на внутренней поверхности
стенки трубы, м;
λ
ст
– коэффициент
теплопроводности материала отло-
жений на внутренней поверхности
стенки трубы, Вт
⋅
м
–1
.
К
–1
.
Коэффициент теплоотдачи снару-
жи трубы определяется условиями
конденсации теплоносителя, который
подается в межтрубное пространство
УДК 664.013.6:664.013.7:665.3.536.24
Рециркуляция как способ
интенсификации
тепло- и массообмена
при дистилляции мисцеллы
в маслоэкстракционном
производстве
А.В.Федоров,
д-р техн. наук,
В.Н.Марков,
канд. техн. наук,
Ш.К.Тагиев,
А.В. Ефимов
ГНУ ВНИИЖ Россельхозакадемии
Н.Н.Романов,
доцент
Санкт-Петербургский университет
ГПС МЧС России
Электронная Научная СельскоХозяйственная Библиотека