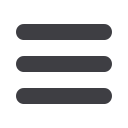

93
QUALITY AND SAFETY
ПИЩЕВАЯ ПРОМЫШЛЕННОСТЬ
8/2004
Количество отказов
шения в основном обусловлены отка&
зами электромагнитных клапанов и
электродов уровня жидкости в дозиро&
вочной станции. При выполнении опе&
раций расстойки и выпечки изделий
основные нарушения связаны с отказа&
ми транспортных систем – роторно&
ленточного укладчика, конвейерного
пода печи, посадчика, выгрузки. Оче&
видно, эти транспортные механизмы
являются самым узким местом выде&
ленных операций.
Как следует из данных, приведенных
в таблице, доля нарушений парамет&
ров технологического регламента при
проведении процесса производства
нарезных батонов за рассматривае&
мый период, обусловленных несовер&
шенством оборудования и его низкой
надежностью, составила 76,40% от
общего количества зафиксированных
нарушений.
Анализ документов об отказах на
исследуемом производстве позволил
определить технологическое оборудо&
вание, которое внесло наибольший
вклад в отклонение технологического
процесса от технологического регла&
мента, а также оценить показатели ча&
стоты отказов и их последствий. Наи&
большее количество отклонений каче&
ственных характеристик продукции
вызвано низкой надежностью дозиро&
вочной станции, делителя, печи, ро&
торно&ленточного укладчика, закаточ&
ной машины. Соотношение отказов ос&
новного технологического оборудова&
ния за исследуемый период показано
на рисунке.
Наиболее часто отмечены отказы
механической части перечисленного
оборудования. В общем количестве
отказов они составили 69,35%. Отка&
зы, связанные с электрической частью
оборудования, составили за исследуе&
мый период 20,94%. Эти показатели
отражают низкую эксплуатационную
надежность используемых машин.
Все указанные случаи привели к
ухудшению качественных характерис&
тик готовых изделий, что зарегистриро&
вано в соответствующих документах.
Анализ показал
большую роль че
ловеческого фактора среди причин
отклонения процесса
(некачествен&
ное проведение процедуры контроля
технологического процесса, наруше&
ние технологической дисциплины, не&
правильное задание параметров про&
цесса).
На стадии разделки теста и формо&
вания заготовок в связи с некоррект&
ными действиями производственного
персонала произошло 34,17% наруше&
ний. Основные из них:
•
ошибки при регулировке делителя,
своевременно не обнаруженные при
контроле массы куска;
•
плохая санитарная обработка де&
лителя, приводящая к торможению
поршня;
•
ошибки в регулировке зазоров ок&
руглителя и закаточной машины.
Основные нарушения на стадии при&
готовления рецептурной смеси связаны
с ошибками при задании расхода жид&
ких компонентов на дозировочной
станции.
Доля нарушений, обусловленных че&
ловеческим фактором на стадиях рас&
стойки и выпечки изделий, незначи&
тельна. В основном эти нарушения
обусловлены ошибками персонала при
задании температурно&влажностного
режима процессов.
Всего за исследованный период на
предприятии отклонения процессов по
вине обслуживающего персонала со&
ставили 19,19 %. Это позволяет сделать
вывод о необходимости максимально&
го автоматизирования производства и
контроля технологического процесса.
Основные причины, вызывающие от&
клонения по вине производственного
персонала, можно сформулировать
следующим образом: неумение оцени&
вать информацию о состоянии процес&
сов; слабое знание сущности происхо&
дящих процессов; технологическая не&
дисциплинированность.
Таким образом, в результате анали&
за имеющихся статистических данных
о нарушениях, зарегистрированных
на представительной выборке техно&
логических процессов и обработан&
ных методами математической стати&
стики,
установлены
основные законо
мерности отклоне
ний
параметров,
вызывающие ухуд
шение
качества
продукции
:
•
снижение каче&
ства готовой продук&
ции в результате от&
клонения технологи&
ческих
процессов
можно интерпретиро&
вать как совокупность
потоков случайных
событий, количество
которых на ограни&
ченных интервалах
времени распределе&
но по закону Пуассо&
на, а время появле&
ния отдельных слу&
чаев по экспоненци&
альному закону;
•
появление каждо&
го случая является
следствием возник&
новения и развития
первичной
цепи
предпосылок;
•
инициаторами
первичных
цепей
происшествий служат
использование техно&
логического оборудо&
вания с конструктив&
ным
несовершен&
ством и низкой эксп&
луатационной надеж&
ностью, нерегламен&
80
70
60
50
40
30
20
10
0
1 2 3 4 5 6 7 8 9 10
Соотношение отказов основного технологического
оборудования за исследуемый период:
1 – дозировочная станция; 2 – роторно&ленточный
укладчик; 3 – печь ПХС–25 М; 4 – делитель А2–ХТН;
5 – надрезчик&опрыскиватель ЛД–151; 6 – посадчик;
7 – тестомесильная машина Р3–ХТИ – 3;
8 – закаточная машина Н8–ХТ3; 9 – выгрузка;
10 – округлитель Т1–ХТН
тированные внешние воздействия на
процесс в результате несанкциониро&
ванных действий и ошибок персонала
при обслуживании оборудования, за&
дании параметров процесса и контро&
ля его проведения.
На основании полученных результа&
тов нами проведено моделирование
ухудшения качества проведения про&
цессов и оценивание вероятности про&
ведения их в регламентированных ус&
ловиях.
Электронная Научная СельскоХозяйственная Библиотека